Fidelity Research FR-64S / FR-66S
Complete Restoration
"Holy Cow! After the complete rebuild of the FR-64S, I believe I am finally getting the original sound. More nuanced, better image specificity. Clean, extended, but not etched.
Very fluid and harmonically correct. No attention to any one band of the spectrum.
Your rebuild and rewiring of the Fidelity Research FR64s is a complete success.
I am still tweaking but holy cow! I put the FR7f cartridge on... ( this one is special) and holy moly the rewire is just phenomenal so elegant and enveloping.
Thank you Mr. RIchard Mak!"
- Nick Judanis

The legendary Fidelity Research FR-64S & FR-66S tonearm is one of the most iconic Japanese tonearms ever made. The engineering and machinery precision is unmatched by many of today's tonearm.
The tonearm, however, has 2 weaknesses. The lubricant and grease they used in the 80s are dried up in all cases. They turn into a thick gooey honey-like substance sticky to the touch, which causes the bearing to seize up. This causes the arm to sound sluggish and dull because what was supposed to lubricate the bearing, act as thick damping glue. FR users sometimes refer to this as "the vintage sound" when in fact, all they are hearing is a sluggish gunked-up bearing.
The majority of FR owners who do not restore their tonearms are not hearing the original Fidelity Research sound. Every FR tonearm should be completely disassembled, relubricated, and restored to its original condition. Once the bearings are restored to their original condition the sound of the FR64/66 is lively, vibrant, dynamic, and with lots of details.
AnalogMagik has performed over 200 Fidelity Research Tonearm restorations as of June 2023.
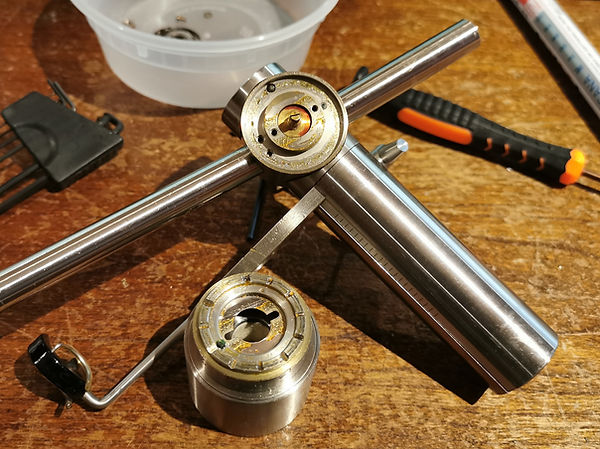
Disassembly of the FR tonearm requires jewelry makers' tools. As can be seen in the photo, the white grease in the coiled spring and the bearing cover has turned into hardened mud, which causes the fine VTF adjustment from operating properly.
The grease on the ball bearing has turned into syrup, which is sticky to touch. Anyone who thinks their arm will sound lively with a gunked up bearing is pipe dreaming. It must be cleaned and relubricated if you want the legendary FR sound of the 80s.

50 yr old grease which has completely hardened. It is harder than wax, and breaks off in chunks. Some disintegrate into a sand-like substance, mixed with a thick goo.

They sticky and gooey old grease saturates the tonearm bearing assembly. All unrestored FR-64S or FR-66S tonearm does not move smoothly. The inner bearing assembly for horizontal movement is literally swimming in thick honey-like old grease which seizes the bearing.
The bearing will not spin and will stop when turned. We disassemble the entire arm and bearing assembly down to individual parts. Every component is soaked in a Swiss Clock Assembly degreaser, a 24-48 hrs process.
Each component is then relubricated with the proper Swiss Clock Maker's Synthetic Lubricant. Different parts require a different type of clock maker's lubricant. Just the lubricants we use cost a few hundred dollars for 25 ml.
After the lubrication with the highest quality, Swiss Synthetic Clock Oil, the bearing will spin smoothly, ensuring tonearm agility as originally intended by the designer.

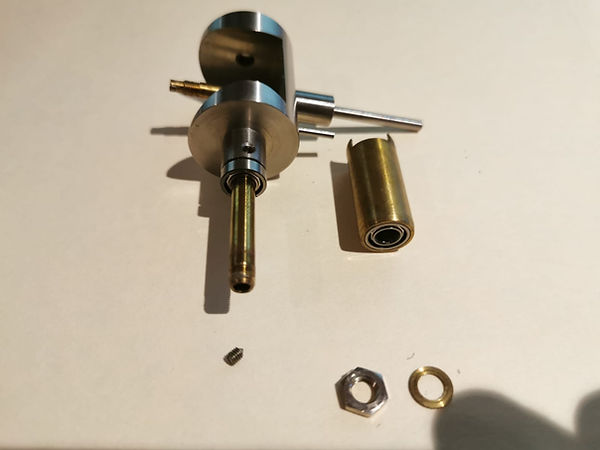

Each Fidelity Research FR-64S or FR-66S bearing is relubricated with Mobius Swiss watchmaker's synthetic oil. 3 different types of lubricants are used, depending on their usage, and location.
The original bearings can also be upgraded to much higher quality ABEC-9 bearings.

The old FR tonearm wire has a jacket that is over 50 yrs old, and very often it breaks at the 90-degree bend at the bearing. We see this very often with FR rebuilds. The jacket material also hardened over time, some literally break off like bread crumbs. The wires are almost always, all oxidized.
Further improvements can be made to the tonearm by eliminating the 11 connections within the tonearm wire. In the FR-64S or FR-66S tonear, the are 11 connections within the tonearm.
-
Cartridge Wires to Pin (Solder Joint)
-
Cartridge Pinouts to Headshell Clip
-
Headshell Clips to Wire (Solder Joint)
-
Wires to Clips again (Solder Joint)
-
Clips to Pins on SME style Headshell
-
Pin to Pin spring-loaded SME DIN connector
-
Pin to Internal Wiring
-
Internal Wire to Din Pin (Solder joint)
-
Din Pin to Female Din of Phono Cable
-
Female Din to Wires (solder joint)
-
Phono Cable Wire to RCA Male Connector (Solder Joint)
No expensive Din to RCA cable will eliminate the 9 unnecessary extra connections which greatly increases measurable resistance and distortions. By eliminating 2 to 10, signal integrity can be improved significantly by having only 2 connections, direct from Headshell Clips to RCA output.
We eliminated all the connections, bypassing the DIN Headshell and DIN connection, with a continuous run of AnalogMagik Reference Tonearm wire, with no connections in between.
Both capacitance and resistance drops significantly once a direct wire connection is made using AnalogMagik Reference Silver Tonearm Wire.
When the bearing is restored, and tonearm cable connections eliminated, the feedback we get from customers is consistent with one another. Typically, a significant improvement in the rendering in minute details, transient attack, and a much livelier presentation.
If you want to hear what the original Fidelity Research sound is like, contact us to inquire about a complete
restoration of your FR tonearm HERE.

When a direct wire is used, we machine a stainless steel cable clamp to secure the cable in lieu of the DIN connector.

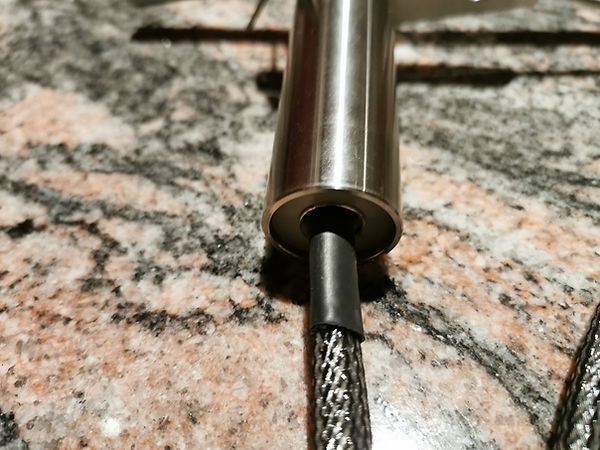
